The growth of micro-coil devices has resulted in the growing urge for custom coil manufacturing. Custom coil manufacturing has always been quite challenging for industries since every client has a different requirement.
In this blog, we’ll explain what is required for the manufacturing process of custom coils in the world of medical equipment. Moreover, we’ll also suggest digital marketing firms for your business either with the help of web marketing or an in-house team to get more leads.
What are Micro Coils?
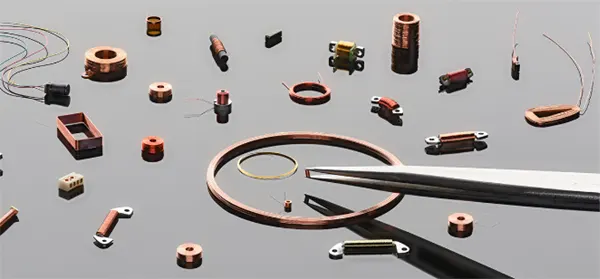
Before anything else, let’s build a clear understanding about Micro coils.
An electrical conductor, such as wire, can be wound into a coil, spiral, or helix to create an electromagnetic coil. A coil’s dimensions and form are customized to meet certain needs. The size and form of a coil are greatly influenced by variables like inductance, resistance, and the intensity of the intended magnetic field. Due to their minimal size, micro coils serve the same purposes as regular coils but frequently require examination and manipulation through the use of a magnifying glass or microscope.
Parameters for Custom Coil Manufacturing
With, it is also very important to find out the key parameters to be kept in mind before going ahead with custom coil manufacturing. Every manufacturing firm has the following three important criteria:
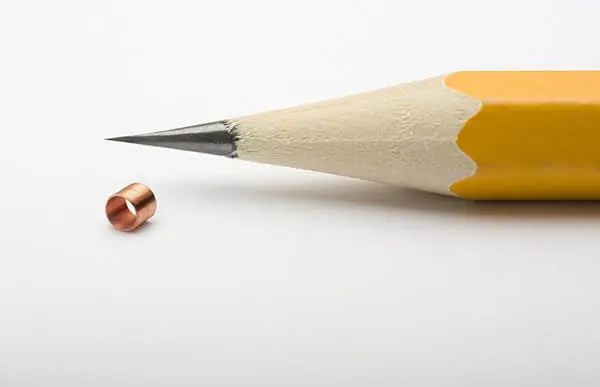
- Cost manufacturing should be less to improve the bottom line.
- Reliability of the product to improve client satisfaction.
- The quality of the coil used in manufacturing should be of better efficiency.
With these three things noted, the most in-demand material used is copper. Materials like aluminum are also used for applications in medical equipment.
Micro Coil Devices: Manufacturing & Challenges
Micro-coil devices have a pretty different manufacturing process. With the changing times, coreless micro coils are having a higher demand. Traditionally wounding the micro coil around the core used to be the only way to manufacture them.
However, with the growth of medical equipment and vein insertion becoming a crucial application of micro-coil devices, coreless coils have become prevalent. A crucial parameter that comes while manufacturing micro coil devices is the thickness of the coil. It determines the number of windings that will present around the core.
When the thickness of the coil reduces, it requires special machinery and expertise to bring about the manufacturing process.
One of the major challenges that are faced during micro coil manufacturing is the integration of it into the devices. Often, due to the thickness of the wire being thinner than the human hair, there are multiple risks associated with the traditional integration methods.
They often include losing out of physical properties or changes in chemical properties. Another potential risk is the oxidation of the micro-coil resulting in the formation of other compounds.
To tackle this, thermo-pressure bonding has come into play. This ensures that the ultra-thin wires don’t face any challenges while being integrated into another wire or into the equipment.
Manufacturing Micro Coil Devices: 4 Criteria to Never Miss Out
Manufacturing of the micro-coil requires the top four criteria that must be followed.
- The experience and expertise to match the client’s requirements.
- Availability of the machinery that’s required to produce custom coils in bulk.
- State-of-the-art technological equipment to stay updated with market trends.
- The required manpower to fulfill the custom-made micro-coil requirements.
Now that we know this, let’s go ahead and see the applications of micro coil devices in the next section.
Applications of Micro Coil Devices In the Medical Field
Micro coil devices have the following applications in the medical field.
- Targeted delivery of the drug due to its high reachability to treat ailments that are deeply seated.
- Temperature tolerance in cancer treatment makes drug delivery successful.
- Capturing brain simulation and monitoring pacemaker data through implants.
- Implemented as sensors for measuring physiological or flow-related parameters.
With numerous applications available in the domain of the medical field, microcoil devices have been highly recommended. Moreover, they have made non-invasive surgeries a reality. This makes them one of the most desired components, thus revolutionizing the medical frontier. And to your surprise, there are several types of coils that are manufactured that cover all the needs in the medical field.
Types of Micro Coils Manufactured
Different types of coils are made so that they reach otherwise inaccessible regions in the body, reduce disruption of regular body functions, reduce energy consumption, and increase the lifetime of implanted devices.
- Miniature Ball Shape Micro Coil
- Miniature Cylindrical Coil 490 Windings
- Miniature Elliptical Coil 9-micron wire
- Miniature Elliptical Coil with Flat Inner Walls
- Miniature Silicon-Core Coil
- Miniature Multi-Layer Coil
- Miniature Cylindrical Coil
- Miniature Elliptical Coil 10-micron wire
- Miniature Cylindrical Coil – 10-micron wire
- Metal Rod Coil
- Miniature Elliptical Coil 12-micron wire
- Self-Bonding Mini Coil
- Flattened Elliptical Coil
- 3-Axis Miniature Medical Sensor (before casting)
- 3-Axis Miniature Medical Sensor (after casting)
- Polyurethane Cast Coil
- Miniature Rectangular Coil
- Miniature Cylindrical Coil – 16-micron wire
So this was all about the micro coils, their different types, and the parameters to manufacture. We hope this blog has helped you understand better.